1. Application:
Mixing Tank|Mixing Reactor|Mixing Vessel for chemical factories is an ideal material for anti acid and alkali corrosion and its surface is very easy to Polish and no contamination to mediums. It's widely used in Petrochemicals, light industry, pharmaceuticals, pesticide, foodstuff, dyes, scientific research etc.
2. Capacity:
Mixing Tank|Mixing Reactor|Mixing Vessel For Chemical Industry capacity: 50 to 30000Liter
3. Structure: Open type (k-type) or closed type( F-type)
4. Material: Vessel: Mild steel with glass lined inside surface: Jacket: Mild steel.
5. Design pressure: Vessel: 0.2Mpa or 0.3Mpa or 0.4-0.6Mpa or 1.0Mpa
Jacket pressure: 0.6Mpa
6. Design Temperature: 200 degree C.
7. Accessories: One complete set of Mixing Tank|Mixing Reactor|Mixing Vessel For Chemical Industry generally with motor with Reducer, Seal (optional: Stuffing box, Single mecheanical seal, Double mechanical seal ), Agitator, Thermometer pocket, bottom discharge Valve.
8. Properties and Advantages:
1) Have the advantages of glass' anti-corrosion and stability and metal's strengh.
Corrosion resistance: Organic or inorganic acid, organic solvent and weak alkaline corrosion (not
including hydrofluoric acid, containing fluorine medium, phosphoricacid, and alkali concentration greater
-than 30% and temperature greater-than or equal 180 Degree Cent. )
2) No contamination: Because Mixing Tank|Mixing Reactor|Mixing Vessel for Chemical Industry inside surface is enamelled so its no contamination to medium.
3) Very easy to wash: Mixing Tank|Mixing Reactor|Mixing Vessel for Chemical Industry inside surface is glass-lined, very smooth, very easy to wash.
4) Pressure resistance:
a) with Packing box: Vessel: Less-than or equal 0.20MPa; Jacket: Less-than or equal 0.6MPa
b) with Single Mechanical seal: Vessel: Equal or less-than 0.30Mpa;Jacket: Less-than or equal 0.6MPa
c) with Double mechanical seal: Vessel: Equal or less than 0.6Mpa; Jacket: Less-than or equal 0.6MPa
5) Operation temperature: 0 to 200 Degrees Cent.
6) Glass layer thickness: 0.8 - 2.0mm
7) Cool shock: 110 Degrees Cent.
8) Thermo-shock: 120 Degrees Cent.
9. Note:
1. Temperature should be slowly changed while heating or cooling Mixing Tank|Mixing Reactor|Mixing Vessel For Chemical Industry avoid damaging glass layer.
2. Mixing Tank|Mixing Reactor|Mixing Vessel For Chemical Industry can not be used in hydrofluoric acid, medium containing fluorine, phosphoric acid, and alkali concentration greater -than 30% and temperature greater-than or equal 180 Degree Cent. )
10. Specification and Demension of Mixing Tank|Mixing Reactor|Mixing Vessel For Chemical Industry
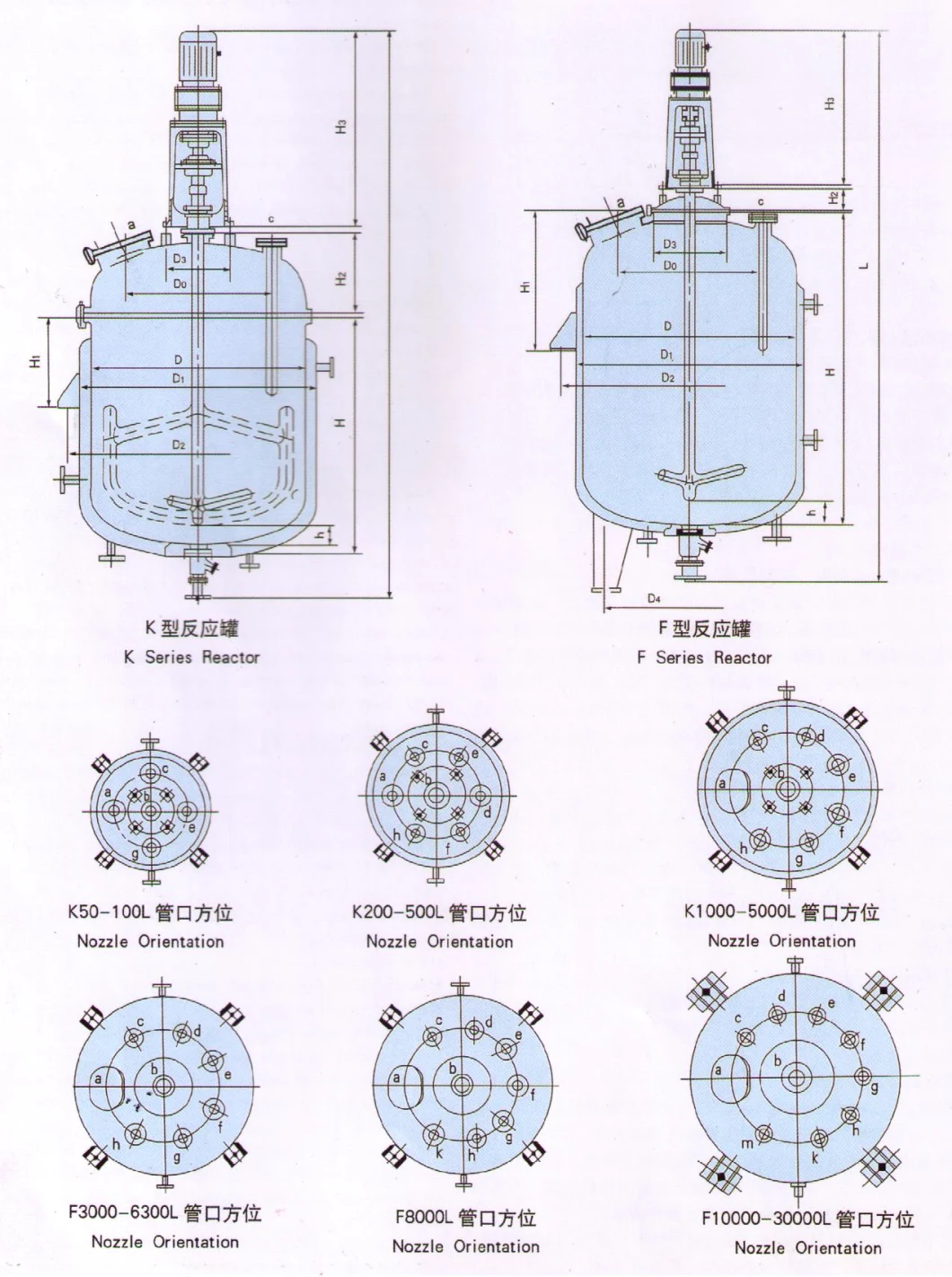
Mixing Tank|Mixing Reactor|Mixing Vessel for chemical factories is an ideal material for anti acid and alkali corrosion and its surface is very easy to Polish and no contamination to mediums. It's widely used in Petrochemicals, light industry, pharmaceuticals, pesticide, foodstuff, dyes, scientific research etc.
2. Capacity:
Mixing Tank|Mixing Reactor|Mixing Vessel For Chemical Industry capacity: 50 to 30000Liter
3. Structure: Open type (k-type) or closed type( F-type)
4. Material: Vessel: Mild steel with glass lined inside surface: Jacket: Mild steel.
5. Design pressure: Vessel: 0.2Mpa or 0.3Mpa or 0.4-0.6Mpa or 1.0Mpa
Jacket pressure: 0.6Mpa
6. Design Temperature: 200 degree C.
7. Accessories: One complete set of Mixing Tank|Mixing Reactor|Mixing Vessel For Chemical Industry generally with motor with Reducer, Seal (optional: Stuffing box, Single mecheanical seal, Double mechanical seal ), Agitator, Thermometer pocket, bottom discharge Valve.
8. Properties and Advantages:
1) Have the advantages of glass' anti-corrosion and stability and metal's strengh.
Corrosion resistance: Organic or inorganic acid, organic solvent and weak alkaline corrosion (not
including hydrofluoric acid, containing fluorine medium, phosphoricacid, and alkali concentration greater
-than 30% and temperature greater-than or equal 180 Degree Cent. )
2) No contamination: Because Mixing Tank|Mixing Reactor|Mixing Vessel for Chemical Industry inside surface is enamelled so its no contamination to medium.
3) Very easy to wash: Mixing Tank|Mixing Reactor|Mixing Vessel for Chemical Industry inside surface is glass-lined, very smooth, very easy to wash.
4) Pressure resistance:
a) with Packing box: Vessel: Less-than or equal 0.20MPa; Jacket: Less-than or equal 0.6MPa
b) with Single Mechanical seal: Vessel: Equal or less-than 0.30Mpa;Jacket: Less-than or equal 0.6MPa
c) with Double mechanical seal: Vessel: Equal or less than 0.6Mpa; Jacket: Less-than or equal 0.6MPa
5) Operation temperature: 0 to 200 Degrees Cent.
6) Glass layer thickness: 0.8 - 2.0mm
7) Cool shock: 110 Degrees Cent.
8) Thermo-shock: 120 Degrees Cent.
9. Note:
1. Temperature should be slowly changed while heating or cooling Mixing Tank|Mixing Reactor|Mixing Vessel For Chemical Industry avoid damaging glass layer.
2. Mixing Tank|Mixing Reactor|Mixing Vessel For Chemical Industry can not be used in hydrofluoric acid, medium containing fluorine, phosphoric acid, and alkali concentration greater -than 30% and temperature greater-than or equal 180 Degree Cent. )
10. Specification and Demension of Mixing Tank|Mixing Reactor|Mixing Vessel For Chemical Industry
Norminal Capacity L | Actual Capacity L | Jacket Heating Area m2 | Reducer | Specification of Packing Box DN | Specification of Drain Valve DN | AgitatorRotation Speed r/min | Size(mm) | ||||||||||||||
Achor Frame | Impeller Turbin Paddle | D | D0 | D1 | D2 | D3 | D4 | H | H1 | H2 | H3 | L | h | Weight Kg | |||||||
Achor Frame | Impeller Turbin Paddle | ||||||||||||||||||||
K50 | 70 | 0.59 | BLD0.75-1 | 40 | 65 | 63/85 | 85/130 | 500 | 350 | 600 | 708 | 270 | / | 480 | 300 | 280 | 923 | 2060 | 50 | 90 | 365 |
K100 | 127 | 0.9 | BLD0.75-1 | 40 | 65 | 63/85 | 85/130 | 600 | 420 | 700 | 826 | 270 | / | 580 | 350 | 315 | 923 | 2250 | 60 | 110 | 435 |
K200 | 241 | 1.5 | BLD1.1-1 | 50 | 80 | 63/85 | 85/130 | 700 | 490 | 800 | 927 | 300 | / | 765 | 350 | 340 | 938 | 2470 | 60 | 130 | 580 |
K300 | 361 | 1.94 | BLD3-2 | 65 | 80 | 63/85 | 85/130 | 800 | 560 | 900 | 1055 | 350 | / | 865 | 380 | 375 | 1098 | 2760 | 80 | 150 | 780 |
K500 | 579 | 2.71 | BLD3-2 | 65 | 80 | 63/85 | 85/130 | 900 | 630 | 1000 | 1156 | 350 | / | 1065 | 400 | 400 | 1098 | 3020 | 80 | 150 | 945 |
K1000 | 1238 | 4.54 | BLD4-3 | 80 | 100 | 63/85 | 85/130 | 1200 | 840 | 1300 | 1488 | 400 | 950 | 1275 | 500 | 480 | 1242 | 3430 | 100 | 210 | 1685 |
K1500 | 1714 | 5.38 | BLD4-3 | 80 | 100 | 63/85 | 85/130 | 1300 | 910 | 1450 | 1639 | 400 | 1080 | 1470 | 600 | 505 | 1242 | 3660 | 100 | 210 | 1990 |
K2000 | 2152 | 7.2 | BLD4-3 | 80 | 100 | 63/85 | 85/130 | 1300 | 910 | 1450 | 1639 | 400 | 1080 | 1810 | 600 | 505 | 1242 | 4010 | 100 | 210 | 2225 |
K3000 | 3200 | 8.9 | BLD5.5-3 | 95 | 125 | 63/85 | 85/130 | 1600 | 1120 | 1750 | 1981 | 450 | 1300 | 1810 | 600 | 590 | 1302 | 4159 | 130 | 240 | 3190 |
K5000 | 5286 | 13.0 | BLD7.5-4 | 95 | 125 | 63/85 | 85/130 | 1750 | 1200 | 1900 | 2131 | 450 | 1400 | 2428 | 700 | 628 | 1382 | 4840 | 130 | 270 | 4455 |
K6300 | 6248 | 15.2 | BLD7.5-4 | 95 | 125 | 63/85 | 85/130 | 1750 | 1200 | 1900 | 2131 | 450 | 1400 | 2828 | 700 | 628 | 1382 | 5240 | 130 | 270 | 4950 |
K8000 | 8038 | 17.05 | BLD11-5 | 110 | 125 | 63/85 | 85/130 | 2000 | 1400 | 2200 | 2502 | 455 | 1650 | 2800 | 780 | 700 | 1455 | 5000 | 150 | 300 | 6210 |
K10000 | 10200 | 22.6 | BLD11-5 | 110 | 150 | 63/85 | 85/130 | 2200 | 1540 | 2400 | 2708 | 510 | 1800 | 2955 | 800 | 750 | 1495 | 5285 | 150 | 330 | 7680 |
F3000 | 3625 | 8.9 | BLD5.5-3 | 95 | 125 | / | 85/130 | 1600 | 1120 | 1750 | 1981 | 600 | 1300 | 2255 | 1060 | 150 | 1302 | 4190 | / | 240 | 2910 |
F5000 | 5858 | 13.2 | BLD7.5-3 | 95 | 125 | / | 85/130 | 1750 | 1200 | 1900 | 2131 | 600 | 1400 | 2911 | 1200 | 150 | 1302 | 4900 | / | 270 | 4100 |
F6300 | 6820 | 15.4 | BLD7.5-4 | 95 | 125 | / | 85/130 | 1750 | 1200 | 1900 | 2131 | 600 | 1400 | 3311 | 1200 | 150 | 1382 | 5330 | / | 270 | 4595 |
F8000 | 9273 | 18.0 | BLD11-5 | 95 | 125 | / | 85/130 | 2000 | 1400 | 2200 | 2502 | 800 | 1650 | 3465 | 1350 | 180 | 1455 | 5510 | / | 330 | 6235 |
F10000 | 11443 | 20.5 | BLD11-5 | 110 | 150 | / | 85/130 | 2200 | 1540 | 2400 | 2708 | 800 | 1800 | 3570 | 1450 | 180 | 1495 | 5690 | / | 360 | 7845 |
F12500 | 13640 | 24.5 | BLD11-5 | 110 | 150 | / | 85/130 | 2200 | 1540 | 2400 | 2708 | 800 | 1800 | 4145 | 1450 | 180 | 1495 | 6450 | / | 360 | 8920 |
F16000 | 17446 | 29.5 | BLD18.5-6 | 130 | 150 | / | 85/130 | 2400 | 1680 | 2600 | 2912 | 800 | 1950 | 4440 | 1450 | 180 | 2180 | 7220 | / | 360 | 11350 |
F20000 | 21750 | 34.4 | BLD18.5-6 | 130 | 150 | / | 85/130 | 2600 | 1820 | 2800 | 3182 | 900 | 2100 | 4700 | 1450 | 230 | 2180 | 7710 | / | 400 | 13545 |
F30000 | 32520 | 42.7 | BLD22-7 | 140 | 150 | / | 85/130 | 3000 | 2100 | 3200 | 3788 | 1100 | 2400 | 5240 | 1600 | 280 | 2200 | 7620 | / | 450 | 19860 |
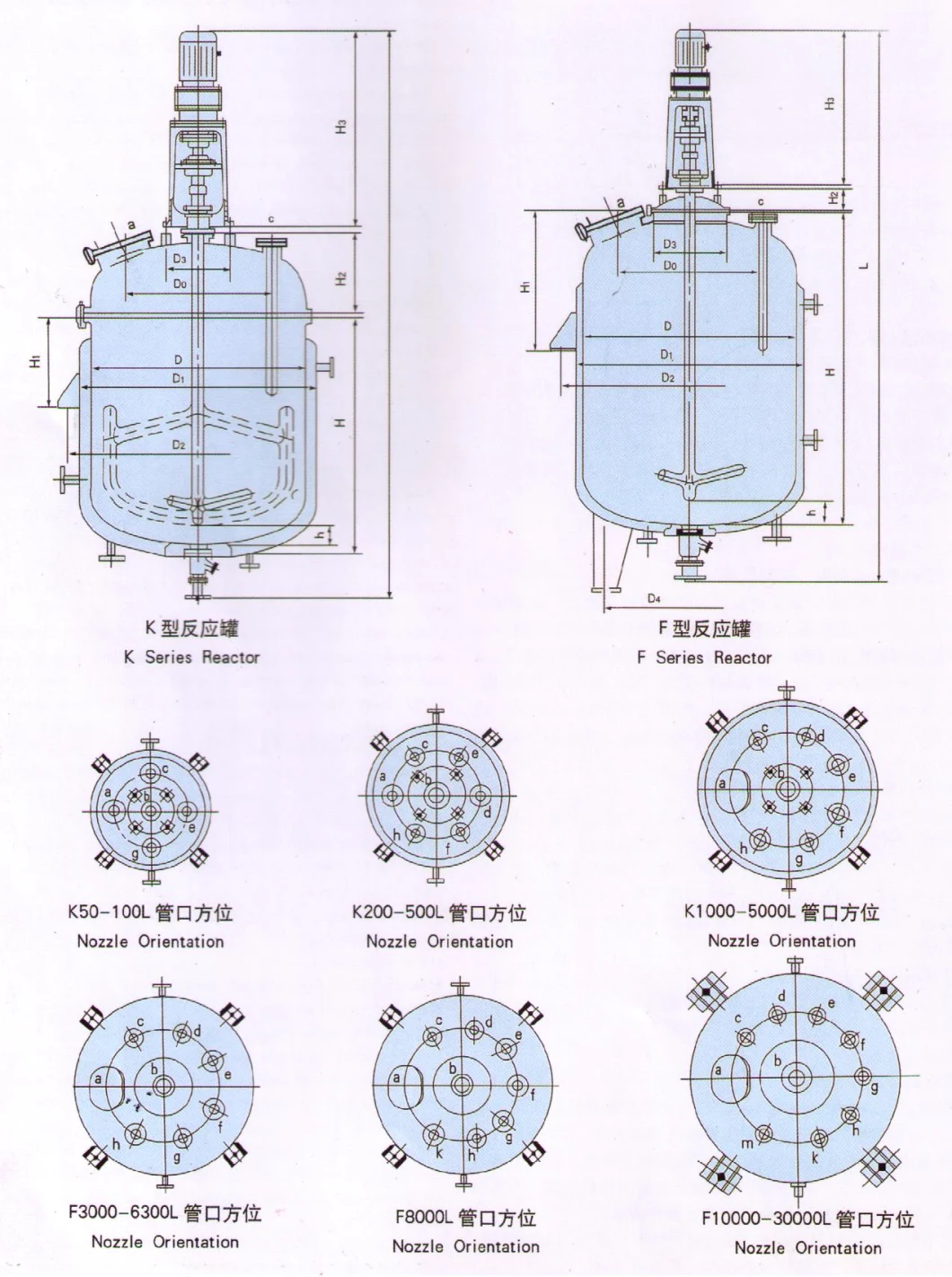